Quality Control Sustainability
Basic Concept
At GOLDWIN, we aim to create products and services of value that benefit customers based on our corporate mission to “realize a fulfilling and healthy lifestyle through sports.” As part of this, we strive to ensure product safety and improve quality. From the design process to ordering materials, production, and inspections of finished products, we comply with relevant laws and regulations, and pursue a level of quality that ensures customer satisfaction. At the same time, we reflect point-of-sale customer feedback in our product manufacturing activities. With the belief that “there is true value in the invisible,” we feel a responsibility for ensuring the peace of mind and comfort of people who enjoy sport, and for providing products that can even improve competitive performance. Our aim is to continue delivering high-quality sports-oriented products.
Promotion Framework and Person Responsible
Our Quality Assurance Department, with the General Manager of the Quality Assurance Department having responsibility, oversees quality control initiatives for the entire group. In addition to formulating rules of operation and managing numerical targets, the Quality Assurance Department also holds monthly Quality Meetings while working to deepen collaborations with the Sourcing Department, RD&D Department, Production Engineering Department, and Customer Service Center. The Sourcing Department is in charge of sharing and requesting quality-related information from suppliers.
Each of these measures are reported on to management at monthly meetings of the Sourcing Headquarters, which are attended by the President and Representative of Board, and the Senior Managing Director. Information on quality-related claims lodged with the Customer Service Center is also distributed as needed to all managers, from general managers and up, including management executives.
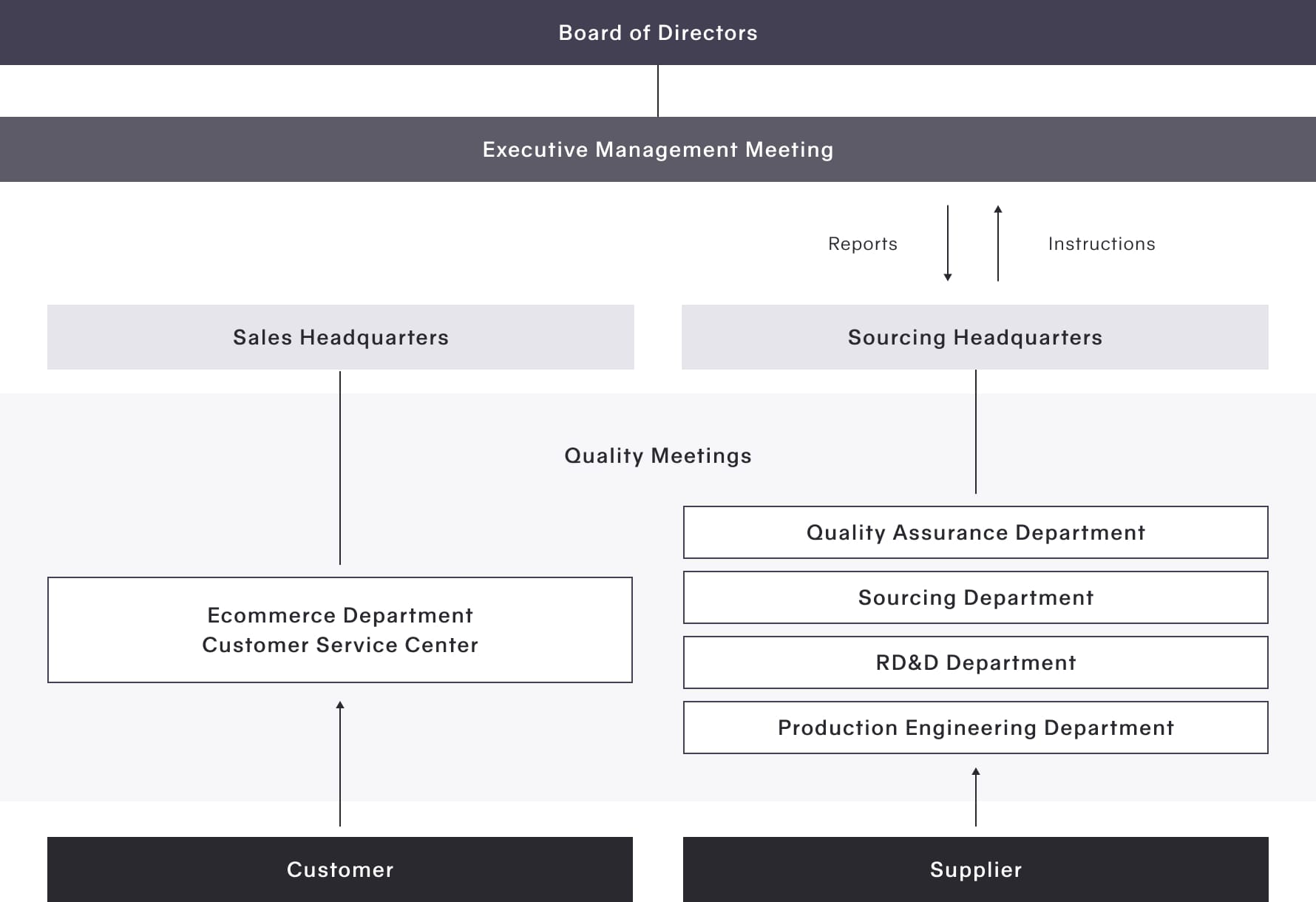
Quality Control System
At GOLDWIN, we have established original Quality Standards that define uniform quality standards for our Group, which suppliers are required to understand with an in-depth level of knowledge. The Quality Standards comprise the four areas of Product Quality Control Guidelines, Product Quality Inspection Guidelines, Materials Quality Control Guidelines, and Materials Quality Inspection Guidelines, and apply to all products we carry. We have established a management system able to deliver high quality to customers with verifications and inspections based on these standards in each process of product planning, production preparation, production, shipment, and acceptance. Based on our Code of Conduct for GOLDWIN Suppliers, we asked more than 300 partner factories to comply with these standards by FY 2022. In FY 2022, we reviewed some of the Quality Standards and reworded expressions that were ambiguous.
Guidelines | Concept |
---|---|
Product Quality Control Guidelines | Guidelines for operation of product quality control. Rules for all aspects of manufacturing, from materials and selection of production factories to quality and safety control during manufacturing. |
Product Quality Inspection Guidelines | Guidelines for product quality inspections. Rules for inspection practices, from manufacturing to shipment and delivery. |
Materials Quality Control Guidelines | Guidelines for operation of materials quality control. Rules for overall operations regarding the inspection and safety of fabric and other materials. |
Materials Quality Inspection Guidelines | Guidelines for materials quality inspections based on standards. Rules for visual inspection and performance testing of materials. |
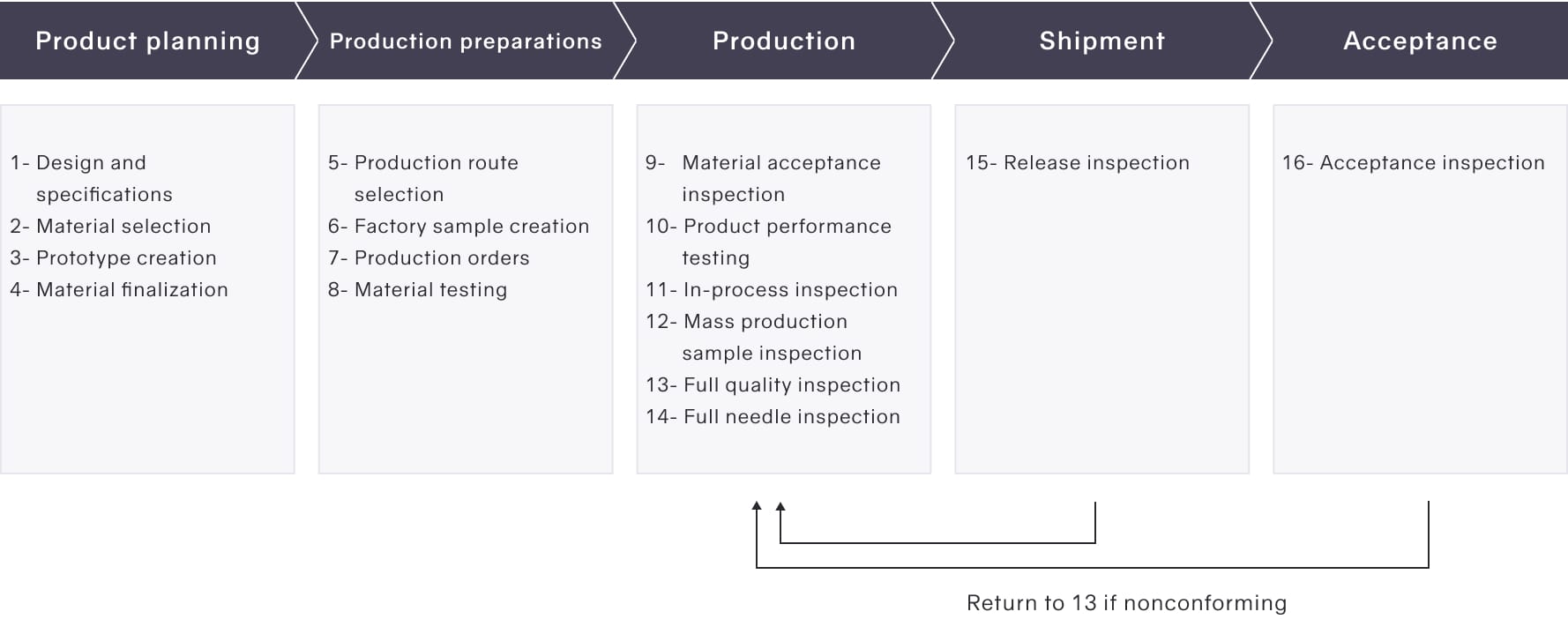
Product Safety
GOLDWIN has established the following four quality standards for managing the safety of its products.
Quality standards for safety | Concept |
---|---|
1. The GOLDWIN Restricted Substance Management Regulations and related laws and regulations must be observed. | In complying strictly with laws and regulations, we strive to provide safe products by incorporating not only Japanese laws and regulations but also overseas regulations. |
2. No substances are used that may cause skin irritation, eczema or rashes due to physical, chemical or other factors. | Since our products are sportswear and outdoor wear, we consider it our mission to ensure that they are always comfortable to use, taking into consideration that they can be used in harsh conditions, such as prolonged use or wet or sweaty conditions, during which skin lesions or other affections may easily occur. |
3. Hazardous objects such as scissors, needles, metal fragments, and other items that may cause harm to the human body are strictly controlled. | We consider that preventing contamination by scissors, needles, metal fragments, and other foreign objects is the most important requirement in maintaining confidence. Our thorough controls to prevent such contamination also leads to improvement of quality. |
4. The safety of children’s clothing is thoroughly controlled. | The safety of children’s clothing is a matter of course for us as a manufacturer. Given that incidents involving children’s clothing may be serious more often than clothing for adults, we thoroughly collect, recognize, and share information on safety control that is specific to children’s clothing. |
Strengthened Quality Control at Supplier Factories
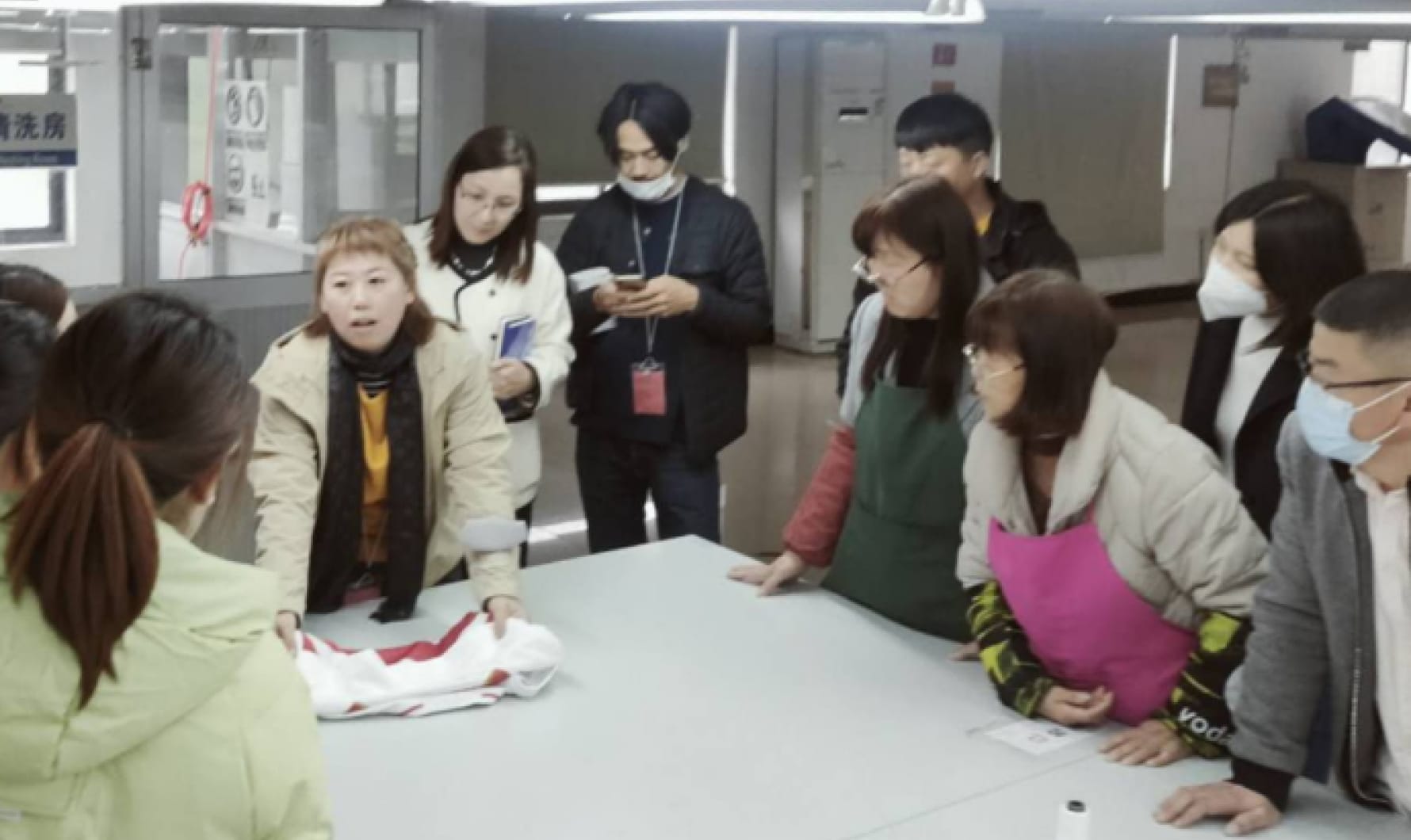
We send specialists to our supplier factories inside and outside Japan to improve quality while providing direct instruction on quality control and production engineering.
In FY 2022, we sent specialists to four factories a total of 12 times. Quality meetings are held every season, where we describe inspection defects and returns and ask for improvements. In terms of production technology too, we check and develop processing methods for new materials at our “mother” factory in Toyama, and based on that expertise, we provide guidance and technology to our production factories. We also field requests from our suppliers for guidance on difficult materials, and we work closely with them. With our rate of overseas production currently at more than 90%, the importance of global quality control measures is increasing. We continue to hold regular quality meetings with our main supplier factories outside Japan, with a total of 14 meetings held with eight companies in FY 2022. We aim to increase corporate value for both GOLDWIN and supplier companies by providing products that customers can feel reassured using through strengthened quality management in cooperation with supplier factories.
Recall handling in the event of product defects
At GOLDWIN, we follow the recall handling procedure below to minimize the possibility of incidents occurring or increasing due to product defects.
- Cease sales and withdraw products from distribution channels and stores
- Provide appropriate information on risks to consumers
- Replace, rectify (inspect, repair, etc.), or accept products already purchased by consumers
In the event of a recognized product defect or incident, the relevant department and Quality Assurance Department collaborate to respond promptly while prioritizing the prevention of harm to customers in line with the Recall Procedure shared companywide.
Overview of Recall Procedure
- The person who receives a report of a product defect communicates promptly with the relevant department.
- The relevant department gathers facts on the incident and shares the information with the Quality Assurance Department.
- A decision is made to recall products in line with the Recall Decision Guidelines and, in the case of a serious incident, a Recall Headquarters is established.
- Products are recalled (the relevant department prepares the response, notifies everyone at once, and the whole company implements the recall).
- The progress of product recovery is monitored and reports are created.
- The relevant department and Sourcing Department collaborate to investigate the cause and formulate measures to prevent recurrence.
- The results of the recall and measures to prevent recurrence are communicated throughout the company.
- The recall is discontinued when the product recovery rate reaches 100%.
In FY 2022, a total of 17 recalls were implemented. None of them were recognized as a serious incident.
Employee Education on Quality Control
With the understanding that employees are the ones who maintain the high quality of products, we provide employees with ongoing education on quality control. We provide a full range of programs tailored to the occupation level, with a focus on people engaged in procurement.
Training | Applicability | Training hours per person (minutes) | Participants (persons) | Training purpose and content |
---|---|---|---|---|
Basic knowledge of quality labeling (composition labeling & handling labeling) | Sourcing Headquarters employees | 40 mins | 81 | Explanation of basic labeling methods according to the textile goods quality labeling regulations under the Household Goods Quality Labeling Act |
Examples of complaints and how they are dealt with | Sourcing Headquarters employees | 50 mins | 44 | Explanation of quality control procedures based on the Quality Standards flow chart and sharing of complaint details |
Product inspection workshop | Labeling managers | 450 mins | 14 | Explanation of manufacturing and the role of product inspection based on the Quality Standards flow chart |
Product inspection workshop | Persons in charge of inspecting recycled products | 300 mins | 8 | Explanation of defective items and measurement methods for product inspections and education on inspection procedures and standards |
Quality control and testing standards | Sourcing Department employees | 660 mins | 2 | Explanation of quality standards and GOLDWIN’s approach to quality |
JIS regulations | GOLDWIN TECH LAB employees | 240 mins | 3 | Explanation about JIS applications |
Testing method for waterproof shoes | Sourcing Department employees | 60 mins | 2 | Sharing of information on testing methods |
Restricted Substance Management
The GOLDWIN Group strives to protect customer and employee safety, and reduce impacts on the global environment, in every one of our products. When using the chemical substances that play essential roles in product manufacturing, we thoroughly manage the substances in every process to prevent contamination with harmful substances.
To strengthen our management globally, we formulated the GOLDWIN Restricted Substance List Compliance in April 2021 in consideration of the laws and regulations of each country where we do business, from Europe and beyond. This list clarifies the restricted substances and restriction levels in all products handled by our group and the materials used in their manufacture. We require suppliers, who deliver products and materials to us, to understand these regulations, and ask that they comply with them and manage their subcontractors accordingly. We have established a management framework in the supply chain, and by FY 2022, we had signed a Memorandum of Understanding for the GOLDWIN Restricted Substance Management Regulations with more than 300 suppliers. The Quality Assurance Department also arbitrarily conducts spot verification testing by a third-party organization to periodically check the status of restricted substance management by our suppliers, and recommends corrective measures if any restricted substances are detected.
GOLDWIN Restricted Substance List (RSL)
The following GOLDWIN Restricted Substance List (RSL) applies to all products supplied to GOLDWIN and our Group companies and to the materials, components, and raw materials used in those products. We share this list within our company and our supply chain to ensure proper management and inspection for compliance with the GOLDWIN Restricted Substance Management Regulations and the RSL.
The RSL is updated as needed in light of social trends and regulatory trends in each country. As far as our supply chain is concerned, we always keep informed of the latest version, and we comply with the limits and other requirements specified in the RSL as well as all relevant laws and regulations required for our products in each country.
Responsible Product Labeling and Advertising Initiatives
It is essential that we provide accurate product information so that our customers can be confident that they are buying quality products and services. The GOLDWIN Group complies with all relevant laws and regulations, and is committed to product labeling and advertising that does not cause misunderstandings.
In terms of the Act against Unjustifiable Premiums and Misleading Representations in particular, which applies to all products, we are working to assign a person in charge of labeling in every department. The Quality Assurance Department has created a Collection of Important Labeling Examples that promotes awareness of specific expressions and terminology. It has distributed this collection to persons in charge of labeling for them to use as guidelines when creating documents for external use in each department.
We comply with the following laws and regulations.
- Household Goods Quality Labeling Act
- Act against Unjustifiable Premiums and Misleading Representations
- Act on Securing Quality, Efficacy and Safety of Products Including Pharmaceuticals and Medical Devices
- Act on the Promotion of Effective Utilization of Resources
- Food Sanitation Act
- JIS standards
- Association of Japan Sporting Goods Industries (JASPO) guidelines
- Guidelines for Environmental Representations
Future Issues
Our unending objective is to deliver higher and higher quality, which we will achieve by continuing to implement quality control initiatives and fulfilling our corporate social responsibility. Our constant aim is to become a trusted company for our customers around the world through the provision of safe and reliable products.
As part of efforts to strengthen our global response, the Code of Conduct for GOLDWIN Suppliers—the global standard we launched in FY 2021—is on track, and we aim to continue its stable operation. We will also continue efforts to reduce complaints and the defect product return rate, and to lower the environmental impact of the supply chain.
In recent years, progress has been made in the development of new products and new materials, and we pursue quality on a daily basis, including by conducting our own original testing in addition to conventional quality inspections.