Occupational Health and Safety Sustainability
Basic Concept
We are committed to upholding management that places first priority on employee health and safety. We have established occupational health and safety regulations, and in addition to preventing work-related accidents and illnesses among employees, we actively ensure their safety and health, and we promote the creation of comfortable, employee-friendly workplaces.
Promotion Framework
We have established Health and Safety Committees for the purpose of holding discussions to ensure our employees can work safely and securely. In addition to improving the workplace environment and preventing occupational accidents from occurring, the Committees protect the health of employees and serve as a forum for employees to actively think about their own health and propose improvements. In accordance with the Industrial Safety and Health Act, we have established committees in the Tokyo, Toyama, and Osaka regions where we have offices with 50 or more employees. One committee member is selected from each department, and meetings are held once a month.
Occupational health and safety at stores across Japan is overseen by the Sales Promotion Department. Information on accidents and incidents at stores is compiled by the General Affairs Department, and reported to the Executive Management Meeting by the Deputy Director of the General Administration Headquarters, who chairs the Tokyo Region Health and Safety Committee.
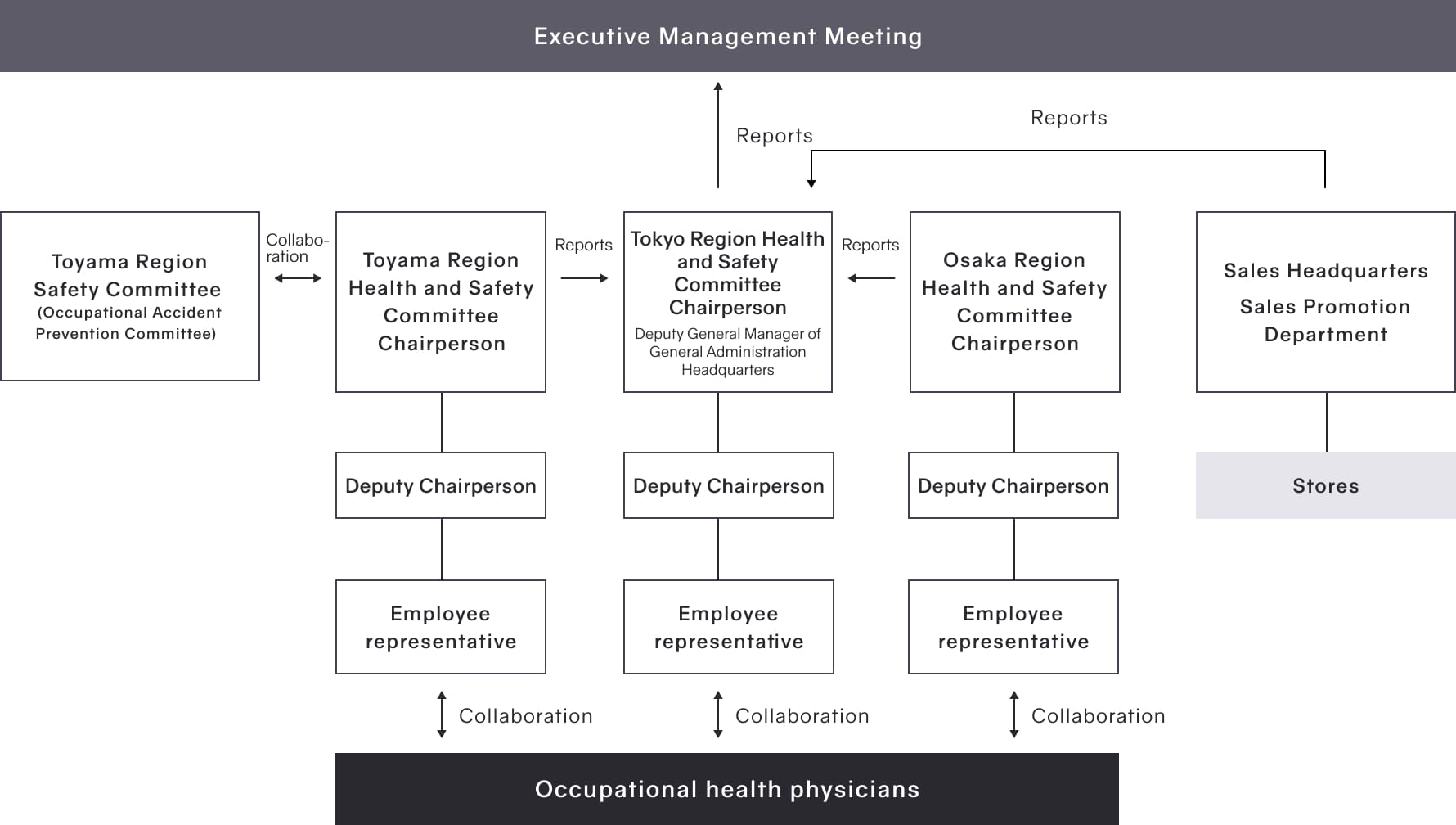
Committee | Meeting frequency | Composition | Description |
---|---|---|---|
Health and Safety Committees | Tokyo Region Toyama Region Osaka Region Monthly meetings |
Chairperson (Deputy Director of the General Administration Headquarters), Vice Chairperson (General Manager of the General Affairs Department), Administrative Office (General Affairs Department), Employee Representative Members (persons in charge from each division) | To protect the safety and health of workers, formulates the Safety and Health Management Plan and conducts adequate investigation and deliberation on important matters, including fundamental measures for preventing danger or health hazards to workers (causes of occupational accidents and measures for preventing their recurrence, etc.) |
Initiatives for the Prevention of Occupational Accidents
At Goldwin, the Health and Safety Committee in each region plays a central role in preventing occupational accidents. Given the nature of our business, we have had no fatal accidents since our founding, and the majority of occupational accidents are those involving vehicles while commuting to and from work. As the number of directly managed stores increases, information on hazardous areas identified in stores and near misses is shared among those involved to help prevent accidents.
In the Toyama area, we have been practicing thorough safety management by providing regular practical training on hazardous operations, such as for compressors, automatic cutting machines, grinders, organic solvents, boilers, and forklifts.
Health and Safety Inspections
To detect any occupational health problems in the workplace at an early stage, we conduct inspections of the internal environment using a Workplace Inspection Checklist through committee activities. The Workplace Inspection Checklist sets weekly and monthly inspection points, and is used when patrolling the company and checking on the workplace environment. In addition, in the Toyama region, we conduct risk assessments, and in FY 2023, 31 locations were evaluated as areas requiring special attention. Manuals have also been prepared and managed which clearly state the safety procedures for using compressors, automatic cutting machines, grinders, organic solvents, boilers, forklifts, and other special equipment that are used in some of our operations.
FY 2019 | FY 2020 | FY 2021 | FY 2022 | FY 2023 | ||
---|---|---|---|---|---|---|
No. of occupational accidents (incidents) | Work-related accidents | 9 | 8 | 5 | 9 | 10 |
Commuting accidents | 4 | 0 | 7 | 3 | 1 | |
Total | 13 | 8 | 12 | 12 | 11 | |
Number of occupational accidents resulting in lost time (persons) | 0 | 3 | 1 | 4 | 4 | |
Number of occupational accidents not resulting in lost time (persons) | 13 | 5 | 11 | 8 | 7 | |
Number of fatalities due to occupational accidents (persons) | 0 | 0 | 0 | 0 | 0 | |
Lost-time accident frequency rate (%) | 0.00 | 0.68 | 0.23 | 0.87 | 0.87 | |
Lost-time accident severity rate (%) | 0.00 | 0.01 | 0.01 | 0.04 | 0.01 |
Future Issues
We will continue to prioritize employee health and safety, and strive to prevent occupational accidents from occurring or reoccurring. Currently, information is appropriately shared among those concerned, but going forward, in order to raise the awareness of each and every employee, information managed on an office basis will be shared across offices to help prevent any accidents from reoccurring.